Abstract
We present a passive fluid transmission based on antagonist pairs of rolling diaphragm cylinders. The transmission fluid working volume is completely sealed, forming a closed, passive system, ensuring input-output symmetry and complete backdrivability. Rolling diaphragm-sealed cylinders provide leak-free operation without the stiction of a traditional sliding seal. Fluid pressure preloading allows for bidirectional operation and also serves to preload the gears or belts in the linear-to-rotary output coupler, eliminating system backlash end-to-end. A prototype transmission is built and tested for stiffness, bandwidth, and frictional properties using either air or water as working fluids. Torque transmission is smooth over the entire stroke and stiction is measured to be one percent of full-range torque or less. We also present a tendon-coupled design where the rolling diaphragm is inverted from its normal orientation; this design does not require shaft support bushings, tolerates misalignment, and can be made out of substantially soft materials. Actuator units and a passive transmission are demonstrated using this new soft cylinder design.
Additional Content
Human-Robot Interactions
When building robots that interact closely with humans, it is important to make the arms as light as possible. With heavy arms, soft and delicate interaction with people is not possible. Because motors are heavy, electric-powered robot arms with human-like arm speed pose challenges when interacting with people. Using multiple-stage gearboxes allows the use of lighter motors, but these gearboxes slow down the arm and increase the friction in the joints, leading to shaky, “robotic” motion.
To avoid this problem, we have developed a fluid-filled transmission that allows the electric motors for each joint to be located inside the body, instead of mounted in the arms. The transmission is much lighter than the electric motors it displaces, so the arms are lighter, and can move faster. In fact, most animatronic robots use pneumatic or hydraulic cylinders for exactly this reason: keeping the arms light. But consider how a hydraulic robot interacts with the environment: if the arm hits an obstacle, the fluid pressure rises, increasing the contact force rather than yielding to the contact; the control valves don’t move and the pump doesn’t spin backwards—we say that a hydraulic system is not backdrivable. If you blow into your garden hose, the valve will not turn backwards by itself. This makes hydraulic robot interaction with humans stiff and awkward. One solution is to add force sensing at every joint and pressure sensing in every hydraulic line. By feeding back this information, it is possible to create softer interactions, but the sensing and control demands lead to complicated designs, and because the controller must wait for sensor data before acting, achieving high speeds and soft interactions simultaneously is very challenging.
The following video shows a robot arm that we have built using our new backdrivable and low friction transmission. The arm is light and fast, and the very low transmission friction allows for delicate and precise movements. These properties allow for natural motion and compliant physical interaction with people. This robot arm was designed and built by Tianyao Chen, Peter Whitney, and Jessica Hodgins.
Low-Friction Fluid Transmission
On account of the very low friction in our transmission, we can operate the robot arm by connecting it to an identical copy of itself, which serves as a direct input for the puppeteer. The pair of identical robot arms in the previous video are connected only by pairs of pneumatic tubing: there are no motors, valves, sensors, or electronic controllers.
Figure 1 illustrates the general concept of the transmission. The secret to its performance is the use of rolling diaphragms to seal the cylinders instead of o-rings. These diaphragms provide very low friction—the total static friction of the cylinders is nearly zero—and a continuous seal, which prevents any fluid leakage. Traditional o-ring seals, which slide along the bore of the cylinder, would have high friction, leading to jerky motion.
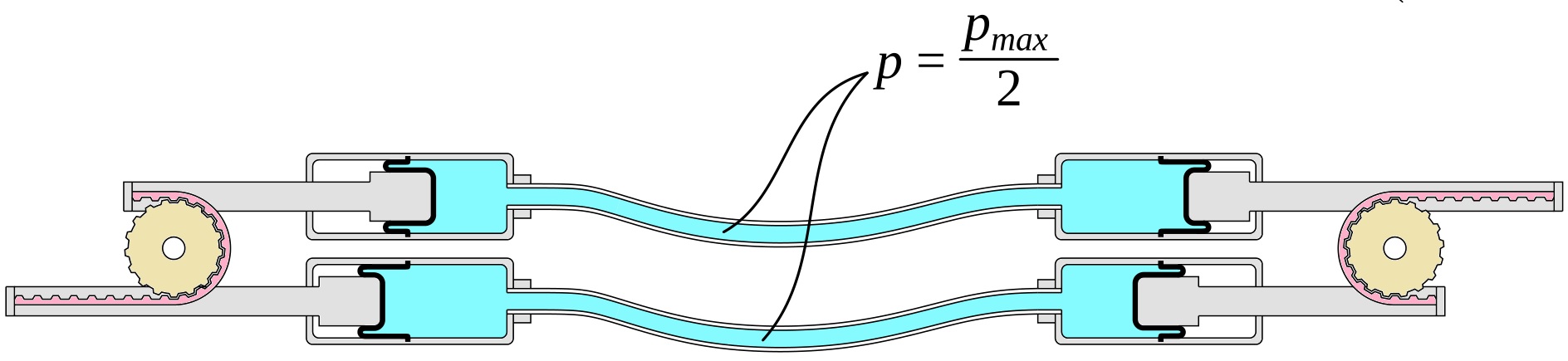
The following video, submitted with the paper, shows the basic function of the rolling diaphragms, and demonstrates a single transmission, operated, in turn, with both air and water. When the transmission is filled with water there is almost zero lag between the input and output because water, unlike air, is not compressible. It is actually possible to feel textures through the transmission; e.g. if you move the input handle so that the output handle rubs against a rough surface, you will feel the bumps at the input. The technical paper provides experimental measurements of the quality of this haptic performance.
Copyright Notice
The documents contained in these directories are included by the contributing authors as a means to ensure timely dissemination of scholarly and technical work on a non-commercial basis. Copyright and all rights therein are maintained by the authors or by other copyright holders, notwithstanding that they have offered their works here electronically. It is understood that all persons copying this information will adhere to the terms and constraints invoked by each author’s copyright. These works may not be reposted without the explicit permission of the copyright holder.